Floating furring walls
I read your two questions and answers about
floating walls with great interest. I am about 20 miles from Aurora and have
exactly the same requirements. I also have one other problem, which I suspect
is rather more common though. I have pipes, air ducting and other obstructions.
In some places these run along the edges of the walls just below the ceiling.
I do not see how to anchor the top of the wall because of the obstruction
and would be very interested in anything you may be able to tell me about
the techniques for dealing with this type of situation.
If I understand your question correctly, you would
like to know how to frame in around your ductwork and how to fasten the top
of the wall up against the concrete wall yet still maintain the floating wall
integrity.
The use of floating wall construction is common in areas where a home may be
built over expansive clay soil. In a basement situation, the concrete floor
is separate from the concrete foundation so the floor could move upward. For
this reason, partition walls are constructed to float 3" off the treated
base plate. To learn more about floating partition walls, click here.
However, furring walls or walls butted up against the foundation can be secured
to the concrete directly. This makes it nice when casing around pipes, air ducts,
or other items that might be up at the ceiling line. The bottom of the wall
still has to have a 4 1/2" space between the bottom plate and the
concrete floor slab. The base plate (treated 2x4) attached to the floor with
3" concrete nails or by using a stud gun will yield a 3" clearance
for expansion. Click here
to see a diagram.
There are a few things to keep in mind when considering how to fur out the
concrete walls. You could use either metal or wooden studs. If you opt for wood,
then be aware that treated wood will need to be used wherever the wood comes
in contact with concrete. You could hold the furring studs out from the concrete
wall in order to eliminate the use of treated material. You will, however, need
treated lumber for a 3/4" ledger board attached to the concrete wall near
the bottom plate of the floating wall (or 1 1/2" which would require you
to notch your studs). This ledger board is required to secure the floating wall
at the bottom so the wall will not swing out into the room. You will need to
toenail the bottom plate to this ledger board. In this situation the foundation
wall is basically used to support the floating wall. Knowing that you can use
the foundation as a support to anchor to should make the project go a bit smoother.
Also, depending on the type of insulation used to meet the energy code*, it
is possible that the furring studs could be 2x2's.
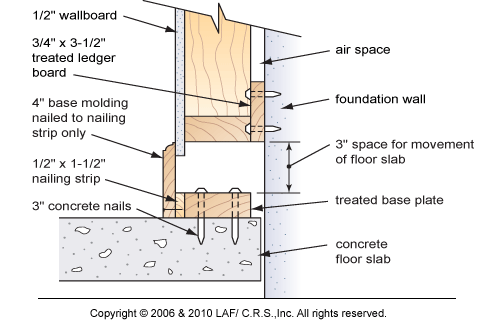
The previous paragraph described an alternative method to the standard floating
wall construction shown in the floating partition wall diagram. However, you
still have to install treated base plates so you have something to which you
can fasten your 4" base moulding. I recommend you install these base plates
prior to the construction of the furring wall. It is crucial that your base
plate and wall be plumb.
To accomplish this, lay the base plate down without nails and measure from
the top of this plate to the underside of the floor joist. This measurement
will be used for wall construction. Measure for all walls and be sure to allow
for the 3" clearance. Then find a straight 2x4 (long enough to reach the
floor and the floor joist), a 6' level, and a helper. Have your helper
stand on the base plate holding the 2x4 against the base plate; place the level
on the inside of the 2x4 to plumb it. Once it is plumb, mark the floor and the
underside of the floor joist and/or backer boards or nailer (small pieces of
lumber nailed between joists)—whatever you plan to nail the top plate of
the wall to. Before nailing to the base plate, make sure that any inside, outside,
furring, and partition walls are at 90 degrees. A framing square comes in handy
for this. When you are satisfied, nail the base plate in place.
Or . . . steel studs could be used. Keep in mind that steel stud construction
requires different tools and techniques. To learn more about steel construction,
get a copy of my book, Build Smarter with Alternative Materials, from
the shopping
mall on my web site. Chapter 4, "Framing Materials,"
sub-chapter "Steel Framing," will give some insight to steel frame
construction. Now the big decision is whether to use wood or steel studs.
*The furring along the concrete wall(s) may require insulation. Check with
your local building department to determine if insulation is required and how
much. Framing a short wall to the underside of the obstructions can box in pipes,
ductwork and other obstructions. Provide a treated ledger board on the foundation
wall to fasten a bottom framework to and then build your floating wall from
there. If the state or local energy code requires R-19 insulation, normally
a 2x4 wall spaced about 2" from the concrete foundation wall can be used.
This will allow you to install the R-19 insulation and will deal with a foundation
wall that is not perfectly straight and true. The floating wall is not a structural
wall so you can frame it at 24" on center. It supports the framing, insulation,
wiring, and drywall. However, 16" on center gives more support for wallboard
and helps to eliminate any damage to it between framing studs from those mysterious
accidents—such as kids wrestling.
The finished rough opening for doors—on a 30" door—should be 32"
plus 1 1/2" for both jambs, plus the thickness of your base mouldings (both
sides), say 1", and another 1/2" for extra space for the base moulding to slide
up behind the doorjambs. This will allow 3/4" on either side for shims when
installing the door jambs. Your total for the rough opening, if using 1/2" base
moulding, would be 35" wide. Normally the finish height of the rough opening
would be 6' 10 1/2"; again, this depends on your ceiling height. There is one
last point to consider: the casing around the door. Your base moulding also
has to slide up behind the casing, so the casing has to be built out away from
the wall, providing clearance on the backside of the casing and the face of
the base moulding. The easiest way to accomplish this is to put jamb extensions
(wooden strips) on both the jambs and walls. Hold the extensions back from the
edges of the jambs by 1/4" when installing. Then attach the second extensions
to the backside of the casing on the heel side (the thickest side)—this
way you can sand the two together. Remember to hold the extensions up 4" from
the bottom of the casing and door jamb to allow the base moulding to slide upward.
To understand more about framing rough openings and jamb extensions, I recommend my book, Remodeling A Bathroom. Chapter 2, "Demolition and Framing," and
Chapter 5, "Working with Wallboard," outline the proper procedures
in-depth and feature great photos and diagrams.
To order Build Smarter with Alternative Materials and/or Remodeling A Bathroom, click here or click the purchase button below!
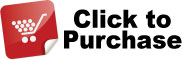
If you are installing a bathroom in an expansive soil environment, click
here
to update the floating wall construction to conform to an installation of
a bathroom.
Copyright © 2001, 2005, & 2006 LAF/C.R.S., Inc. All rights reserved.
Question answered
by Leon A. Frechette.
[ Back to Top ]
|